
Case StudyManaging farm robots at scale: Real-time control for agricultural operations
Challenge
A robotics startup developing autonomous weeding machines for agriculture had an internal debug interface used by engineers. As the robots were deployed to customer farms, the interface proved too complex and technical for field operators. The need was clear: replace the engineer-centric tooling with an operator-friendly dashboard that supported real-time control, exception handling, and safe, scalable management across multiple active fields.
Solution
Planorama collaborated closely with the client to design a new operator interface purpose-built for real-time agricultural workflows. Key elements included:
- User-Centric Dashboard Redesign: We stripped away legacy engineering functions and focused the interface on task-relevant workflows like system bring-up, real-time field management, and exception handling.
- Manage-by-Exception Philosophy: We designed information-dense dashboards featuring real-time video feeds, map views, and alert systems that allowed operators to focus only on meaningful events—reducing noise and cognitive load.
- Domain-Aware Design Collaboration: Leveraging our team’s IoT and real-time systems expertise—including motors, sensors, connectivity loss, and asynchronous data—we collaborated with the client’s engineering team to define robust normal and exception recovery workflows.
- Safe, Actionable Interfaces: Each screen was tailored to allow safe, timely decision-making by non-technical users even in high-pressure or unexpected scenarios.
Outcome
Planorama’s transformation of the client’s interface delivered operational and business value at multiple levels:
- Increased Operator Efficiency: Field operators could now manage multiple fields and machines simultaneously with confidence, boosting throughput and reducing oversight burden.
- Reduced Downtime: Clear exception workflows and real-time visibility enabled faster reactions to anomalies, minimizing robot idle time and avoiding crop damage.
- Higher Customer Satisfaction: The easy-to-use interface required minimal training, helping the client scale deployments and support with lower operational friction.
- Bottom-Line Impact: By enabling precision, exception-based management and increasing system uptime, the new dashboard contributed to significant improvements in operational efficiency and cost savings.
By combining UX strategy with engineering fluency, Planorama delivered an interface that brought real-time robotics into the hands of non-technical agricultural workers—bridging the gap between innovation and practical field adoption.
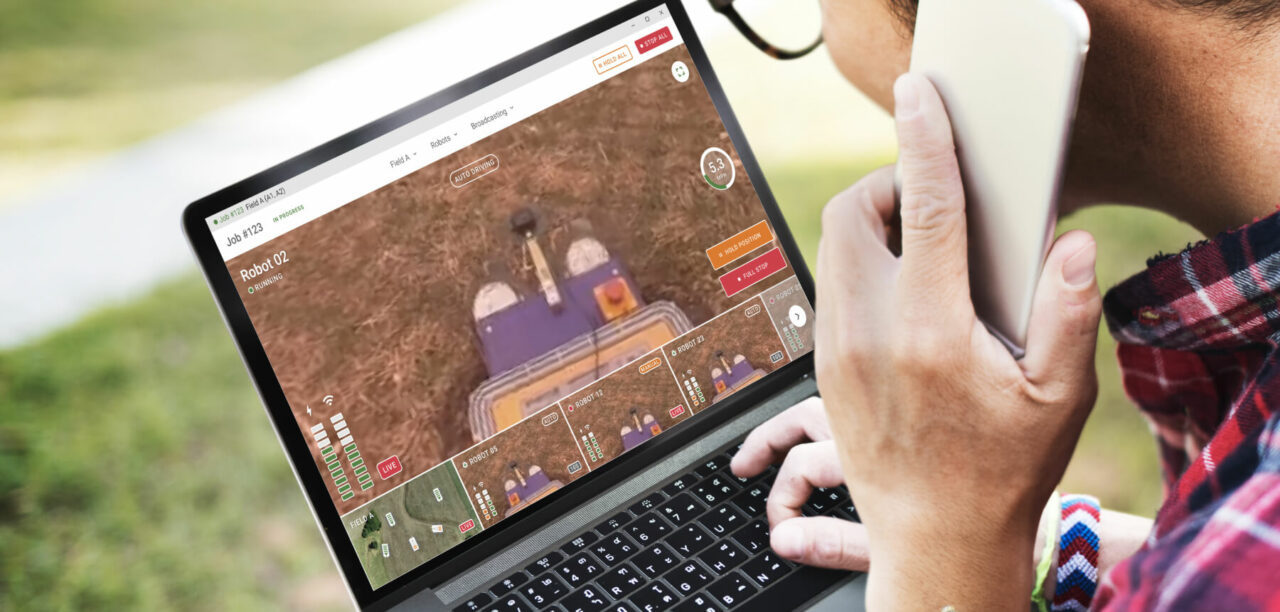

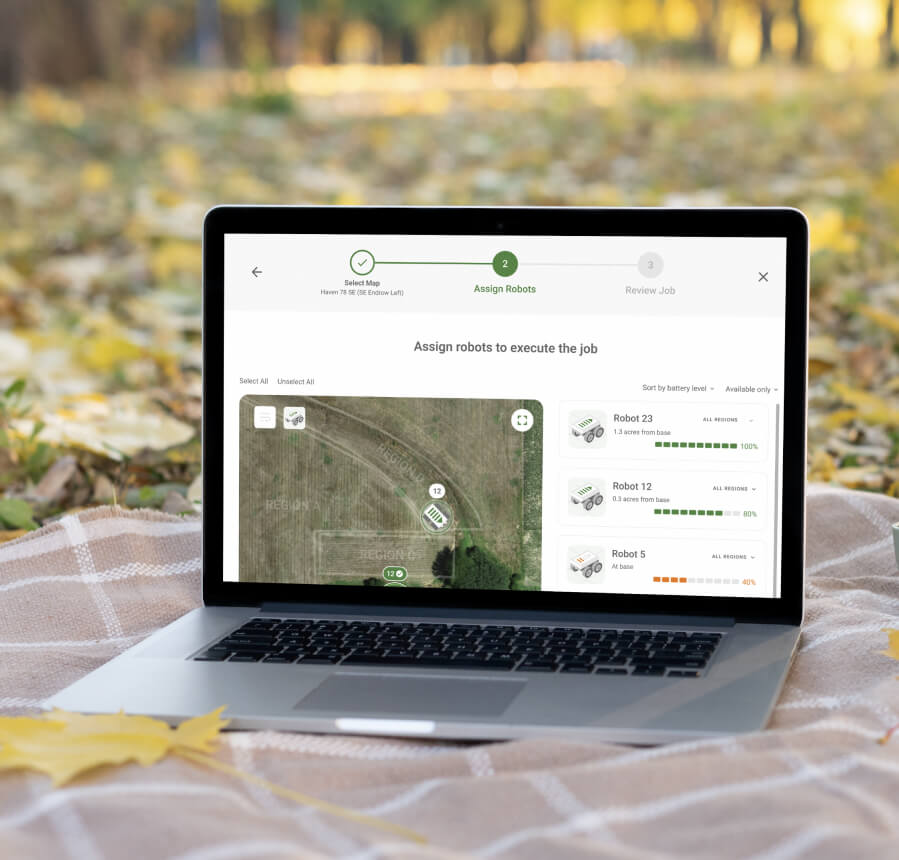